Introduction
Overmolding is a manufacturing process in which multiple components are combined into one finished product through an injection molding process. An injection molding machine combines various materials, such as thermoplastic elastomers and thermoplastic materials, into plastic parts that boast improved resistance and performance characteristics. Overmolding is an invaluable technique in manufacturing. It offers numerous advantages over its counterparts, such as increased design flexibility and decreased secondary operations requirements. Overmolding allows manufacturers to produce complex parts using multiple colors and materials – something previously impossible through other manufacturing methods. We will discuss its advantages in more depth here as well as why it can be an economical way of producing over-molding plastic parts.
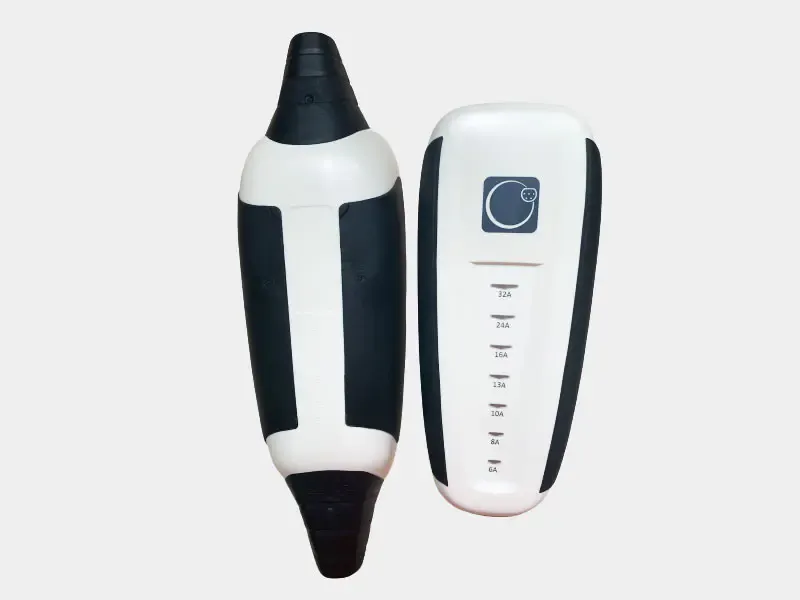
II. What is Overmolding?
Overmolding is the practice best manufacturing method of applying one material over another to create a final product with specific properties. This process typically begins with an injection molded plastic part being placed into another mold cavity where another thermoplastic material, such as thermoplastic elastomers or thermoplastic materials then molded over it, fusing into one, integrated piece.
Various over-molding processes
such as insert molding, two-shot molding, and co-injection molding. Insert molding involves inserting an existing metal or plastic component, such as an automobile part, into another mold cavity where it will then be over-molded with another material. Two-shot molding entails using two distinct materials in one mold to form one complete part while co-injection molding (commonly known as sandwich molding) involves simultaneously injecting two separate substances into an injection mold – these processes enable more complex parts with unique features not achievable through other manufacturing methods.
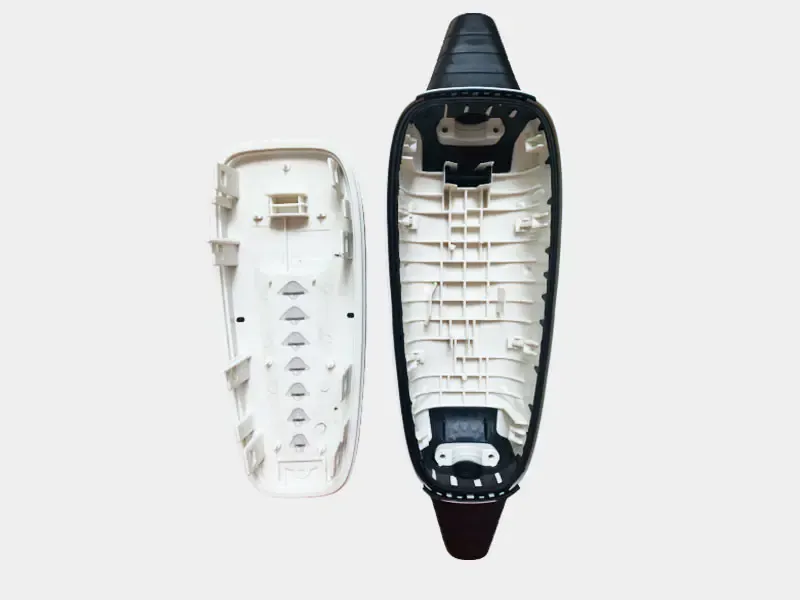
III. Advantages of Overmolding
Overmolding offers several advantages over other production processes, such as:
Improved Product Performance:
Overmolding allows manufacturers to develop parts with enhanced resistance against impacts, chemicals, and environmental elements. By using multiple materials in one part, over-molding allows manufacturers to tailor the properties to meet specific performance criteria; for instance, plastic handles for tools can be over-molded with thermoplastic elastomers for improved comfort during use.
Lower Labor Time and Costs:
Overmolding allows manufacturers to cut manufacturing time and costs associated with producing an end product by eliminating secondary operations like bonding or assembly that require time-consuming or costly secondary processes like bonding or assembly. By creating one integrated part, for example, manufacturers can decrease overall manufacturing time as well as labor costs associated with creating it.
Overmolding provides greater design flexibility:
this process enables designers to craft parts with more complex geometries and unique features that would otherwise not be achievable through other manufacturing methods. By employing different materials and colors, over-molded products can boast increased visual appeal while providing additional functional properties – for instance, product casings can be over-molded using multiple colors and materials to achieve more pleasing designs.
Reduced Need for Secondary Operations:
Overmolding eliminates the need for secondary operations like bonding or assembly, which can take significant time and money to perform. By creating one integrated part instead of two or more components, manufacturers can save both manufacturing time and labor costs associated with creating their finished products.
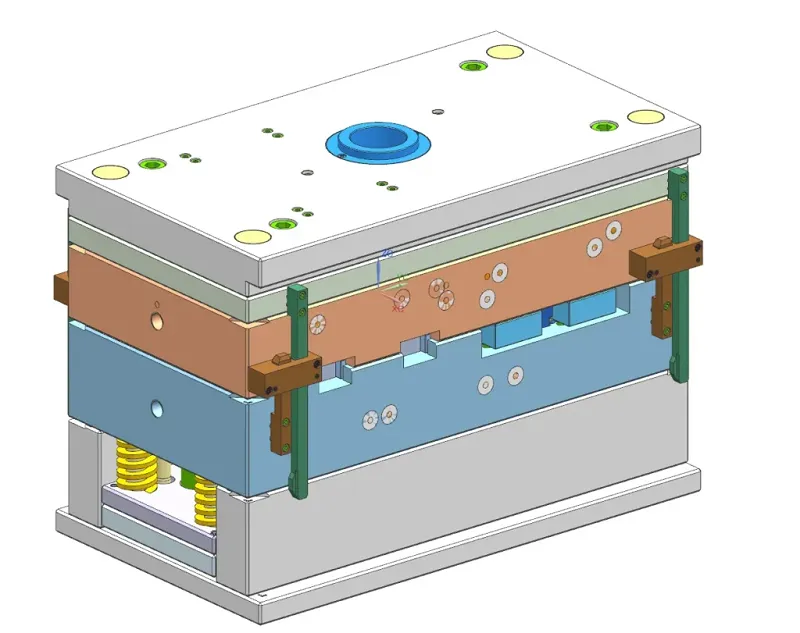
Overmolding offers numerous advantages when it comes to manufacturing plastic parts, especially products requiring improved performance, greater design freedom, and lower manufacturing costs.
IV. How Overmolding Works
Overmolding involves multiple steps that include melting thermoplastic elastomer, materials, alignment, and injection molding. It begins by creating an initial plastic part using an injection molding machine; once placed into another mold cavity it’s placed back into its initial mold where thermoplastic elastomers or acrylonitrile butadiene styrene (ABS) material will be injected to create the final over-molded part.
To create a high quality molded part, initial and second mold cavities must align properly – usually achieved through careful tooling or molding processes. Once aligned, additional material is melted and injected into the second mold cavity where it adheres directly to the original insert molded part, producing one integrated piece.
Thermoplastic elastomers are popular choices for the plastic over molding process over-molding due to their excellent chemical resistance, durability, and flexibility – qualities that make them highly useful across a range of applications from automotive parts, consumer electronics, and medical devices to toys, household appliances, and electronics. ABS resin is another widely-used material for overmolding purposes in particular for consumer products like toys.
Materials used for over-molding must be carefully chosen to ensure they can bond together securely. Their melting temperatures must also be considered to ensure seamless molding processes.
Overall, over-molding requires careful planning and execution to produce high-quality over-molding parts that meet specific performance specifications.
V.Overmolding vs. Other Manufacturing Methods.
Overmolding offers several advantages over other manufacturing methods like single-shot molding and insert molding. The single-shot molding requires using one mold to produce multiple parts simultaneously, which limits design flexibility and creates complex parts composed of multiple materials. Conversely, insert molding requires inserting a pre-molded component into another cavity within another mold cavity – both processes are time-consuming and expensive.
Overmolding allows for the production of complex parts with multiple components by molding them all in the same mold, producing one integrated part without needing secondary processes such as bonding or assembly. Furthermore, this method offers greater design freedom allowing parts with distinctive features or properties to be created more quickly and cost-effectively.
Overmolding can benefit a range of products, including medical devices, plastic handles, and product casings. Overmolding has several applications in medical device production such as creating parts that are durable yet flexible enough to withstand chemicals and environmental factors; overmolding also creates devices with enhanced functionality such as instruments with soft grips that make medical professionals’ work more comfortable.
Plastic handles for tools and appliances can benefit greatly from over-molding, as it allows them to have soft grips which help improve ergonomics and reduce hand fatigue. Product casings used for consumer electronics also take advantage of over-molding; creating parts in a plastic casing with unique features such as multiple colors or textures allows for the creation of parts with visual appeal that could otherwise not exist.
Overmolding offers several advantages over other manufacturing techniques, making it a viable solution for creating plastic parts with improved performance and functionality.
VI. Is Overmolding Expensive?
Overmolding costs can differ depending on various factors, including the complexity of the part, materials used, and production volume; however, the overmolding process remains an economical method of creating plastic parts with improved functionality and performance.
Overmolding can help lower upfront costs by eliminating secondary operations such as bonding or assembly, which decreases manufacturing time and labor costs associated with producing finished products. Furthermore, over-molding allows the creation of parts with unique features and properties not feasible with traditional manufacturing methods, leading to higher-value products with greater returns on investments.
Overmolding may require an initial higher upfront investment due to its specialized tooling and machinery requirements; however, costs of over-molding can be decreased with multi-shot molding techniques which use one mold for creating multiple components within one molding cycle – thus decreasing manufacturing time and labor costs associated with product production.
Overmolding costs tend to be lower than other manufacturing methods due to reduced labor and secondary operations costs, making this an attractive method of plastic part production. Though an initial investment may be higher, its long-term cost savings and improved product performance make the plastic over-molding process an appealing solution.
Conclusion
Overmolding offers several advantages over other manufacturing processes for creating plastic parts with enhanced performance, functionality, and design options. This includes reduced labor costs and manufacturing time as well as improved product performance with no need for secondary operations – making over-molding a cost-effective method to create high-quality parts that meet specific performance requirements.
As part of any manufacturing project, it is wise to explore the potential advantages of over-molding. By combining multiple materials in one part, over-molding allows manufacturers to produce higher-quality products with unique characteristics that cannot be produced using other manufacturing processes.
Overmolding offers many advantages when it comes to manufacturing plastic parts, including enhanced product performance, increased product design flexibility, and lower manufacturing costs. By taking advantage of its many advantages for producing high-quality plastic parts that meet customer demands and stand out in a competitive marketplace, over-molding stands as the ideal solution.