Introduction:
Hot runner systems play a pivotal role in the world of injection molding, revolutionizing the manufacturing process. These systems offer significant advantages over traditional cold runner systems, making them a preferred choice for many industries. In this article, we will provide a comprehensive definition and overview of hot runner systems, highlighting their significance in the field of injection molding.
Definition and Overview of Hot Runner Systems:
Hot runner systems are a type of injection molding technology that facilitates the precise control and distribution of molten plastic material within a mold. Unlike cold runner systems, which consist of channels or runners that carry the molten plastic from the injection molding machine nozzle to the mold cavities, hot runner systems maintain a constant temperature throughout the entire system.
A hot runner system typically consists of a manifold, nozzles, and a temperature control system. The manifold is responsible for distributing the molten plastic to the various mold cavities, while the nozzles deliver the plastic material to the mold. The temperature control system ensures that the plastic remains at the desired temperature throughout the process.
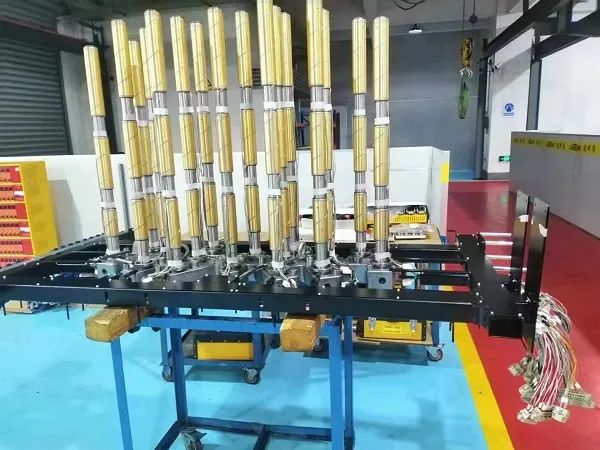
In conclusion, hot runner systems are a significant advancement in injection molding technology. They offer enhanced efficiency, cost savings, improved part quality, design flexibility, and precise process control. By utilizing hot runner systems, manufacturers can optimize production processes, reduce waste, and achieve consistent high-quality parts, contributing to their competitiveness in the market.
II. Advantages of Hot Runner Systems
A. Enhanced Part Quality and Design Flexibility
- Consistent Melt Flow for Superior Part Quality
Hot runner systems excel in providing consistent and uniform melt flow throughout the injection molding process. The elimination of cold runners ensures that the molten plastic reaches the mold cavities without disruptions or variations, resulting in superior part quality. With consistent melt flow, manufacturers can achieve defect-free parts with excellent surface finish, dimensional accuracy, and structural integrity.
2. Design Freedom and Innovation without Runner Constraints
Hot runner systems offer unparalleled design flexibility, allowing for intricate and complex part geometries. Unlike cold runner molds, where runners limit design possibilities, hot runner systems eliminate these constraints. Designers can unleash their creativity and explore innovative designs without compromising functionality. The absence of runners enables the production of complex shapes, thin walls, and intricate features, opening doors to new possibilities in product design.
B. Increased Efficiency and Cost Savings
1. Material and Energy Savings by Eliminating Cold Runners
Hot runner systems eliminate the need for runners, leading to significant material savings. With a cold runner system, excess material in the runners is often wasted or requires regrinding. Hot runners minimize material waste, optimizing resource utilization and reducing costs associated with material consumption. Moreover, the elimination of runners also translates into energy savings as there is no need for cooling or reheating the material in the runners.
2. Shorter Cycle Times for Improved Productivity
The absence of cooling time associated with cold runners significantly reduces the overall cycle time in hot runner systems. Hot runners keep the plastic material at a controlled temperature, eliminating the need for cooling before the next injection cycle. This reduction in cycle time allows for faster production rates and increased productivity, maximizing output and reducing lead times.
3. Reduction in Production Costs
Hot runner systems contribute to cost savings in various ways. The elimination of runners results in material savings, reducing material costs over time. The shorter cycle times achieved with hot runner systems increase production efficiency, enabling manufacturers to produce more parts within a given timeframe. This increased productivity leads to cost savings in labor, energy, and overhead expenses, making the hot runner mold system a cost-effective solution in the long run.
C. Process Control and Optimization.
1. Precise Temperature Control and Optimized Gate Freezing
Hot runner systems provide precise temperature control at every stage of the injection molding process. The temperature can be precisely adjusted in the hot runner manifold and nozzles, ensuring consistent melt quality and accurate filling of the mold cavities. Additionally, hot runners allow for optimized gate freezing, preventing gate vestige and enhancing part ejection, resulting in high-quality finished products.
2. Balanced Melt Flow for Consistent Quality
The manifold system in hot runner systems plays a crucial role in achieving balanced melt flow to all mold cavities. This balanced flow ensures that each part receives the same amount of molten plastic, eliminating variations in part quality caused by uneven filling. By maintaining consistent melt flow, hot runner systems ensure consistent part dimensions, surface finish, and mechanical properties throughout the production process.
3. Manifold System’s Role in Process Optimization
The manifold system, a key component of hot runner systems, allows for the efficient distribution of the molten plastic to the individual nozzles. It helps control the flow rate, pressure, and temperature, contributing to process optimization. The design and layout of the manifold system are tailored to specific mold requirements, ensuring optimum performance and facilitating smooth production operations.
D. Design Flexibility and Innovation.
1. Complex Part Geometries without Limitations Hot runner systems enable the production of complex part geometries that would be challenging or impossible to achieve with cold runner systems. The absence of runners eliminates design constraints, allowing for the creation of intricate shapes, thin walls, undercuts, and other complex features. Hot runner systems empower designers to push the boundaries of creativity and deliver innovative, visually appealing, and highly functional products.
2. Simultaneous Production of Multiple Cavities Hot runner systems offer the advantage of producing multiple parts in a single molding cycle. The ability to fill multiple cavities simultaneously increases production efficiency and reduces cycle times. This feature is especially beneficial when manufacturing high-volume production runs, as it maximizes output and optimizes the use of resources.
3. Competitive Advantages for Diverse Industries The design flexibility, improved part quality, increased efficiency, and cost savings provided by hot runner systems offer significant competitive advantages to manufacturers across diverse industries. Whether it’s automotive, consumer goods, medical devices, or electronics, hot runner systems enable businesses to deliver high-quality products, optimize production processes, and stay ahead of the competition.
By harnessing the advantages of hot runner systems, manufacturers can achieve superior part quality, design freedom, production efficiency, and cost-effectiveness, positioning themselves for success in the dynamic world of injection molding.
III. Comparison with Cold Runner Systems
A. Brief Explanation of Cold Runner Systems
Cold runner systems are a traditional approach to injection molding that utilize channels or runners to deliver molten plastic from the injection molding machine nozzle to the mold cavities. These runners remain at ambient temperature, and after the plastic cools and solidifies within them, they are typically discarded as waste. Cold runner mold requires additional processing steps, such as runner separation and regrinding, which can increase material waste and production costs.
B. Advantages of Hot Runner Systems over Cold Runner Systems
Hot runner systems offer several advantages over cold runner systems, making them the preferred choice in many injection molding applications:
1. Material Efficiency: Hot runner systems eliminate the need for cold runners, reducing material waste. In cold runner systems, the plastic in the runners is discarded as waste, leading to significant material losses. Hot runner systems, on the other hand, ensure efficient material utilization by directly delivering the molten plastic to the mold cavities without the need for runners. This results in material savings and cost reduction.
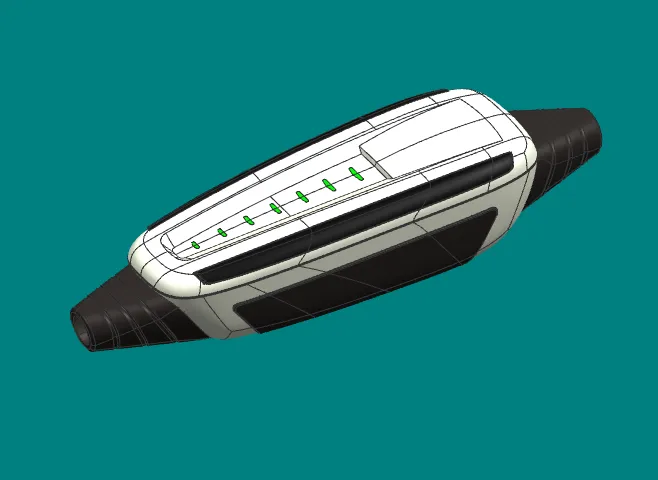
2. Cost Savings: By reducing material waste, hot runner systems contribute to cost savings in terms of raw material consumption. Additionally, the elimination of runners simplifies the production process, reducing the need for additional labor, energy, and equipment for runner separation and regrinding. This streamlined process translates into cost efficiency and improved profitability.
3. Enhanced Part Quality: Hot runner systems provide consistent melt flow and temperature control, resulting in superior part quality. In cold runner systems, variations in flow and temperature can lead to defects such as flow lines, cold spots, and gate blush. Hot runners eliminate these issues, producing high-quality parts with excellent surface finish, dimensional accuracy, and structural integrity.
4. Design Flexibility: Hot runner systems offer greater design flexibility compared to cold runner systems. The absence of runners allows for more intricate and complex part geometries. Designers can create innovative and visually appealing designs without the limitations imposed by runners, opening up new possibilities for product development.
C. Why Hot Runner Systems Have Become the Preferred Choice
Hot runner systems have gained popularity and become the preferred choice in injection molding for several reasons:
1. Improved Efficiency: Hot runner systems optimize production processes by reducing material waste, shortening cycle times, and increasing productivity. The elimination of runners and associated cooling times in hot runner systems allow for faster injection cycles, resulting in higher production rates and improved efficiency.
2. Enhanced Part Quality and Aesthetics: The consistent melt flow and temperature control in hot runner systems contribute to superior part quality. Hot runners eliminate defects and inconsistencies, resulting in parts with excellent surface finish and dimensional accuracy. This enables manufacturers to deliver high-quality products that meet the demands of customers.
3. Cost-Effectiveness: While the initial investment in hot runner systems may be higher, the long-term cost-effectiveness is evident. Material savings, reduced production costs, and improved efficiency lead to significant cost savings over the lifecycle of a project. The enhanced part quality also reduces the need for rework or scrap, further contributing to cost-effectiveness.
4. Design Freedom: Hot runner systems provide designers with greater freedom to explore complex and intricate part designs. The absence of runners allows for more innovative and aesthetically pleasing designs, leading to differentiation in the market and increased customer satisfaction.
In conclusion, hot runner systems offer clear advantages over cold runner systems in terms of material efficiency, cost savings, part quality, and design flexibility. The improved efficiency, superior part quality, and cost-effectiveness have made hot runner systems the preferred choice in modern injection molding applications. Embracing hot runner systems allows manufacturers to optimize their processes, reduce waste, and deliver high-quality products to meet market demands.
IV. Overcoming Challenges and Considerations
A. Addressing Common Concerns and Misconceptions
Hot runner systems, while offering numerous advantages, may raise certain concerns or misconceptions that need to be addressed:
1. Complexity: Some may perceive hot runner systems as complex and difficult to operate. However, advancements in technology and improved system designs have made them more user-friendly and easier to integrate into existing injection molding processes. Training and support from hot runner manufacturers can help address any initial complexity concerns.
2. Cost: The initial investment in hot runner systems can be higher compared to cold runner systems. However, it is crucial to consider the long-term cost savings achieved through reduced material waste, increased efficiency, and improved part quality. A thorough cost-benefit analysis should be conducted to evaluate the return on investment over the lifespan of the system.
3. Maintenance and Repairs: Hot runner systems require regular maintenance to ensure optimal performance. However, proper maintenance procedures and routine checks can help prevent issues and maximize the lifespan of the system. Partnering with reputable hot runner manufacturers who provide timely support and spare parts can address maintenance concerns effectively.
B. Cost Considerations and Return on Investment
When considering the implementation of hot runner systems, it is essential to evaluate the cost implications and the potential return on investment:
1. Initial Investment: Hot runner systems typically have a higher upfront cost compared to cold runner systems. However, it is crucial to assess the long-term benefits, including material savings, improved efficiency, and enhanced part quality, which can justify the initial investment.
2. Material Savings: Hot runner systems minimize material waste by eliminating runners, leading to significant cost savings over time. The reduction in material consumption directly contributes to improved profitability.
3. Increased Efficiency: Hot runner systems reduce cycle times, increase production rates, and optimize resource utilization, resulting in improved operational efficiency. The enhanced productivity and reduced downtime contribute to cost savings and higher throughput.
4. Improved Part Quality: The consistent melt flow and temperature control in hot runner systems ensure superior part quality, reducing the need for rework or scrap. This leads to cost savings and improved customer satisfaction.
C. Choosing the Right Hot Runner System for Specific Needs
When selecting a hot runner system, it is important to consider the specific requirements and objectives of the injection molding process:
1. Mold Design: The hot runner system should be compatible with the hot runner mold design, taking into account factors such as the number of cavities, part complexity, and gate location. Working closely with hot runner manufacturers can help identify the optimal system design for the specific hot runner mold requirements
2. Process Parameters: The selection of hot runner systems should align with the desired process parameters, such as material type, melt temperature, injection pressure, and cooling requirements. Considering these factors ensures the system can effectively meet the production goals.
3. Support and Service: Partnering with reliable hot runner manufacturers who offer technical support, training, and after-sales service is essential. Choosing reputable manufacturers with a track record of quality and customer satisfaction can provide peace of mind and ensure a smooth implementation.
By addressing concerns, conducting a thorough cost analysis, and selecting the right hot runner system, manufacturers can overcome challenges and maximize the benefits offered by hot runner technology. Careful consideration and collaboration with experts in the field can help ensure successful implementation and long-term success in injection molding operations.
Conclusion:
Hot runner systems have revolutionized the field of injection molding, offering numerous advantages over traditional cold runner systems. Throughout this article, we have explored the benefits of hot runner systems, including enhanced part quality, improved efficiency, cost savings, and design flexibility. Now, let’s recap these advantages and reflect on the significance of hot runner systems in injection molding.
Recap of the Advantages of Hot Runner Systems:
Hot runner systems offer several key advantages:
1. Enhanced Part Quality:
Hot runner systems ensure consistent melt flow, resulting in superior part quality with excellent surface finish, dimensional accuracy, and structural integrity.
2. Improved Efficiency and Cost Savings:
By eliminating runners, hot runner systems reduce material waste, shorten cycle times, and increase production rates, leading to cost savings and improved efficiency.
3. Design Flexibility:
Hot runner systems provide designers with greater freedom to explore complex and intricate part geometries, enabling innovation and creativity.
4. Process Control and Optimization:
Precise temperature control, optimized gate freezing, and balanced melt flow contribute to better process control and optimized production.
Encouragement to Embrace Hot Runner Technology:
We strongly encourage businesses in the injection molding industry to embrace hot runner technology. By adopting hot runner systems, manufacturers can optimize their production processes, reduce material waste, improve part quality, and gain a competitive edge. The benefits of hot runner systems, including increased efficiency, cost savings, and design flexibility, can lead to improved profitability and customer satisfaction.
Final Thoughts on the Significance of Hot Runner Systems in Injection Molding:
Hot runner systems have transformed the injection molding industry, enabling manufacturers to produce high-quality parts with efficiency and precision. The advancements in hot runner technology have addressed common concerns, such as complexity and cost, making them more accessible and cost-effective. The consistent part quality increased productivity, and cost savings offered by hot runner systems have positioned them as an integral part of modern injection molding processes.
By embracing hot runner technology, manufacturers can unlock new possibilities for product design, reduce waste, and streamline production processes. The significance of hot runner systems extends beyond the injection molding process, impacting overall business success and market competitiveness.
In conclusion, hot runner systems have proven to be a game-changer in injection molding, offering advantages in part quality, efficiency, and cost-effectiveness. Embracing hot runner technology is a strategic choice that can drive innovation, optimize production, and position businesses for long-term success in the dynamic world of injection molding systems.